Key Fact
Added advantage of fast and easy implementation of new software features
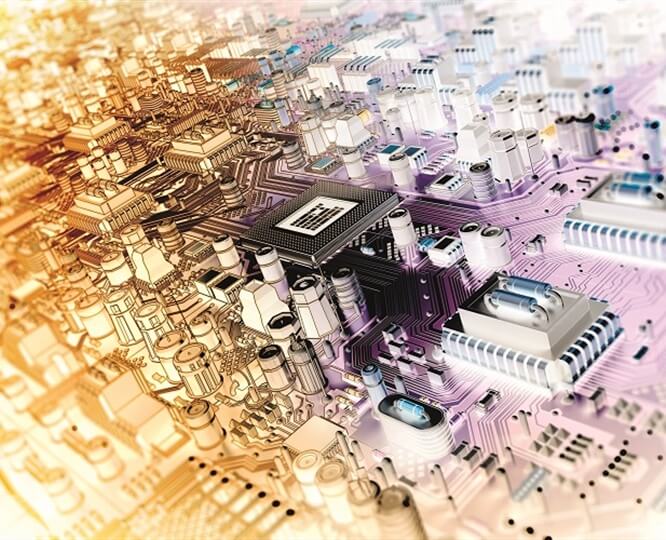
Testimonials
“This new system caters for the easy addition or removal of functionality from the system”
Understand
The Multi Fuel Burner Test Facility (MBTF) in Glasgow, Scotland, is used to test different coal furnace technologies in addition to being capable of testing numerous different types of coal fuel. The plant control system was originally implemented using National Instruments (NI) FieldPoint hardware, and NI Lookout software. Due to global environmental pressures, there is now a requirement to test numerous different ‘clean burn’ technologies and fuels. TBG has implemented a major upgrade to the MBTF software, replacing the existing Lookout code with a more powerful LabVIEW™ system. This new system caters for the easy addition or removal of functionality from the system as may be required by the various burn technologies under test.
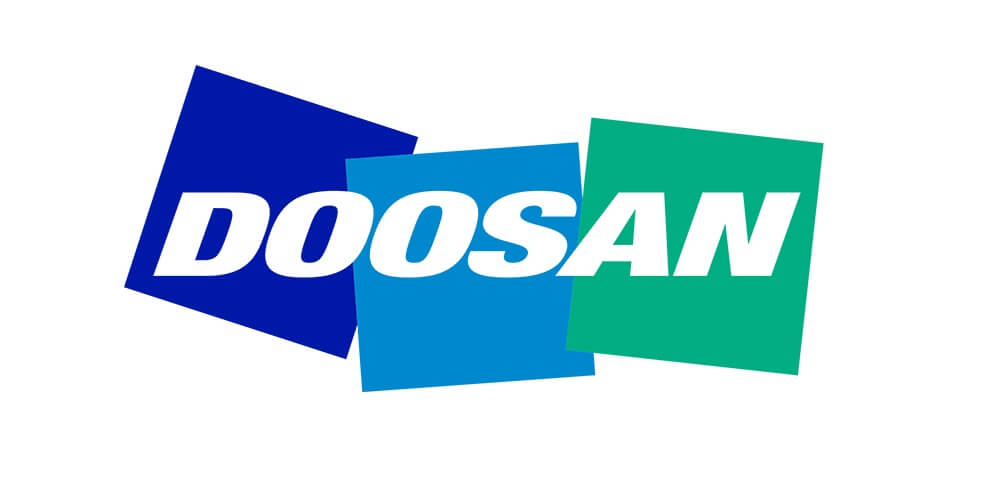
Engineer
The plant comprises more than 450 data channels used for data acquisition and control. Plant control, data analysis and trending are performed by three different PCs: a master PC controls the plant’s hardware, and two remote PCs are used to view the data from all sensors within the plant, producing historical trends and data logs, which are required by the owner of the technology under test and also the Scottish Environmental Protection Agency (SEPA).
Using the original system as software specification, all of the necessary objects, logic and functionality in Lookout were redesigned using LabVIEW, ensuring the new software mimics the look and feel of the original Lookout system. The system is divided into nine sections such as water cooling, furnace ignition or coal transport, allowing the operator to easily switch between each of the different screens.
The main design challenge was to determine the functionality of the original system through analysis of the existing Lookout code. It emerged that understanding the code alone was not sufficient to ensure that the LabVIEW system would operate correctly. As a result it was necessary to obtain a thorough understanding of the mechanics of the system through the study of existing flowcharts, wiring diagrams and hardware schematics. This had the added benefit of allowing us to be more capable at finding faults during the commissioning of the system.
Deliver
Doosan Babcock now use a system that has the same functionality, look and feel as its original Lookout system. It does, however, have the added advantage of fast and easy implementation of new software features that reflect any necessary hardware changes required to the furnace architecture to test future coal burning technologies.
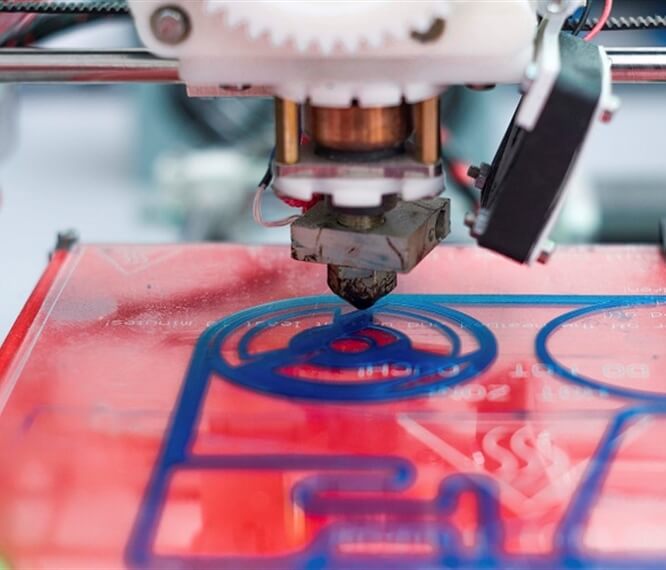