Key Fact
The system was developed using an object-orientated approach in order to maximise the scalability of the test rig
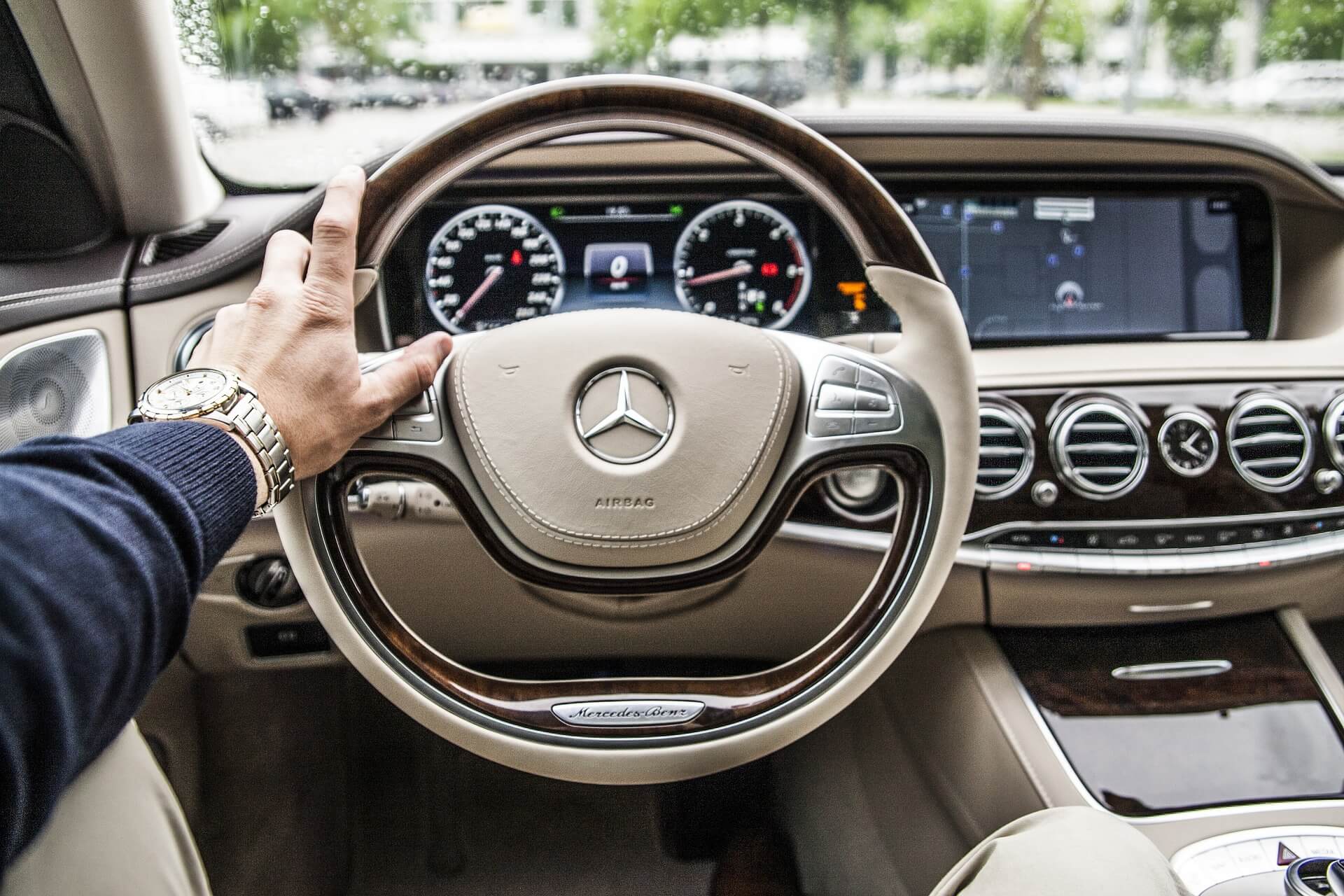
Testimonials
“The new system gives us a huge degree of freedom and significantly reduces the time it takes us to build new test procedures.”
Understand
Our customer is a global supplier of automotive systems, modules, and components to automotive original equipment manufacturers and related aftermarkets. We have provided them with a flexible multi-axis motion test facility capable of controlling up to four individual drives to be utilised in tests performed on Electronic Power Assisted Steering (EPAS) racks, used in a large variety of automobiles. The system provides the capability to determine the quality of their products through measurements such as friction and hysteresis.
Engineer
Design Challenges
The main design challenge in this system was to provide a flexible interface and control architecture that allows our customer to research and design a large variety of tests that can be undertaken using any number of motion axis. Being capable of writing detailed and complex testing scripts through an intuitive user interface allows the customer to rapidly prototype, test and perform custom measurements on any of their EPAS product range.
The next main challenge was to ensure that the software contained safeguards to protect the product samples under test from over application of load or torque. As a result, alarm limits for selected sensors are saved within the motion profiles, so that custom load and position limits can be applied depending on which test is being performed. This eliminates any risk of damage to hardware when developing new tests.
System Design
The system was developed using an object-orientated approach in order to maximise the scalability of the test rig. The system is capable of independently running up to four motion profiles on two rotary and two linear actuators. Typically the software is used to control the application of load or apply a deflection to a test sample for the purpose of calculating stress and performance measurements. In addition to the four motion axis, there is a brake controlled from a calibrated voltage output. This allows the test designers to apply a load/torque onto one end of a steering rack and apply an independent braking torque at the opposite end of the test piece, effectively controlling the torsion. In addition to the control aspects, there is a sophisticated data acquisition routine that acquires data to a log file at high speed for offline analysis in addition to displaying the test results on a live trend screen.
Deliver
Our customer now has the capability to design and run a variety of tests in which there is an unprecedented degree of freedom. As a result of the reduced time taken to develop and build new test procedures, the rig is now under large demand to perform production tests in addition to purely being used as a platform for researching and developing new tests.
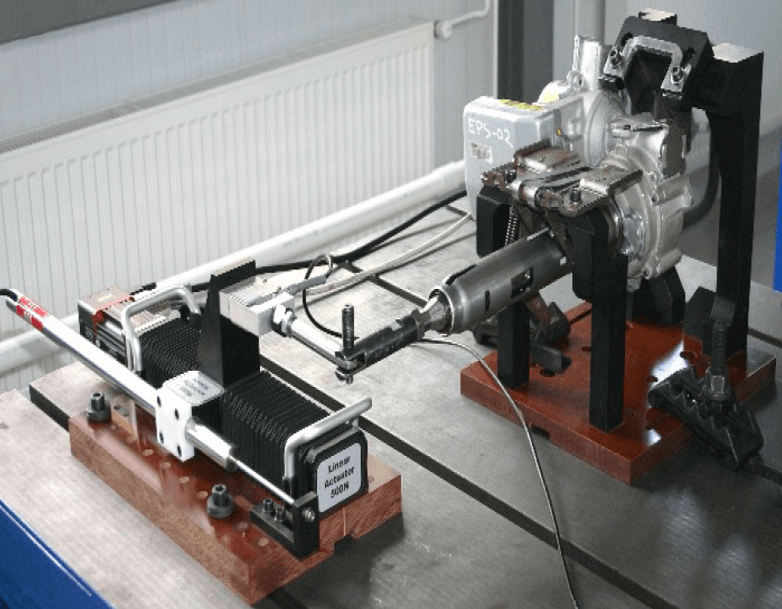
